Water and oil do not mix. How to keep that from happening.
Willard Saysā¦ā¦
Trouble-free ladderpump and cutterdrive operation depends to great extent on sealed, oil-filled housings that contain vital components such as shafts, bearings and gear sets. Lubricating oil, the life blood of these housings must be kept clean and water-free despite having to function while immersed in an environment where water pressure increases with depth. With water all around, lurking, pressing on the housing and seal, constantly testing the integrity of seals, seeking to gain entry at first opportunity to contaminate the oil. Shaft seals are the ākeepers of the gateā standing guard to prevent water intrusion.
We will examine two common shaft seals; lip seals and metallic face seals.
LIP SEALS
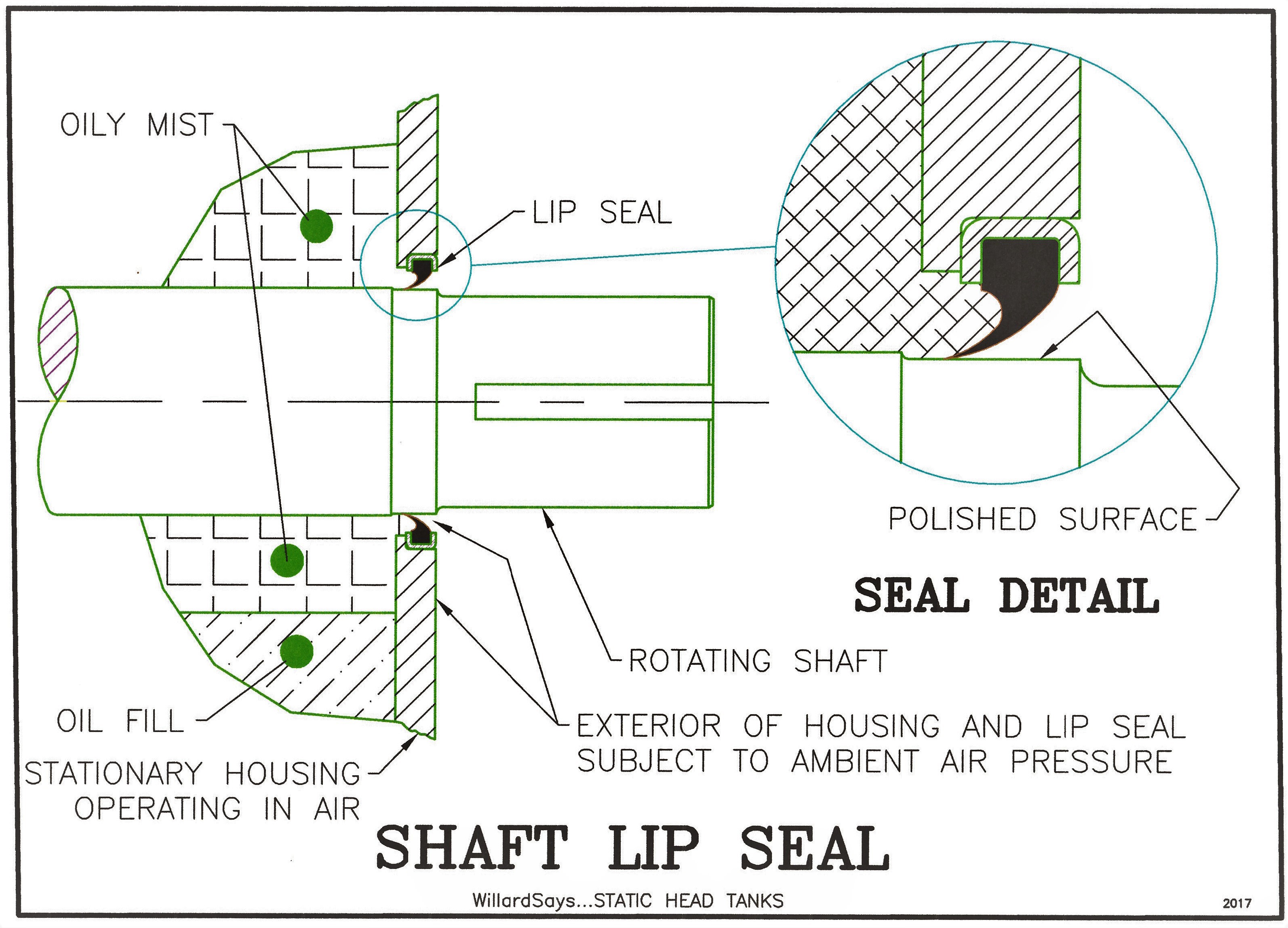
Figure #1 shows a cutaway view of a housing operating in air where pressure inside the housing is the same as the pressure outside.
The flexible tip of the lip seal rides on a polished section of the rotating shaft to keep oil in and contaminants out. This wee bit of contact is all that is necessary under normal conditions, but it does not take abuse very well.
A breather cap fitted to the top of housing allows air to enter or exit as necessary to assure that the differential pressure across the lip seal remains near zero. Differential pressure is the difference between the pressure outside and the pressure inside the housing.
Lip seals will almost certainly fail if the differential pressure across the seal becomes only slightly negativeāthat is when the pressure outside the housing is greater than the pressure inside the housing. These seals protect when subjected to normal outside environmental conditions, however, they may fail if doused with a high-pressure stream of water from a wash-down hose.
Figure #2 shows a housing where the oil level is higher than the seal which results in a positive differential pressure across the seal. If the differential pressure is substantial the lip will bear on the shaft with increased force and likely wear a groove in the shaft.
On the other hand, if the differential pressure is negative as may be the case if the housing is submerged, the seal will leak and allow water to enter.
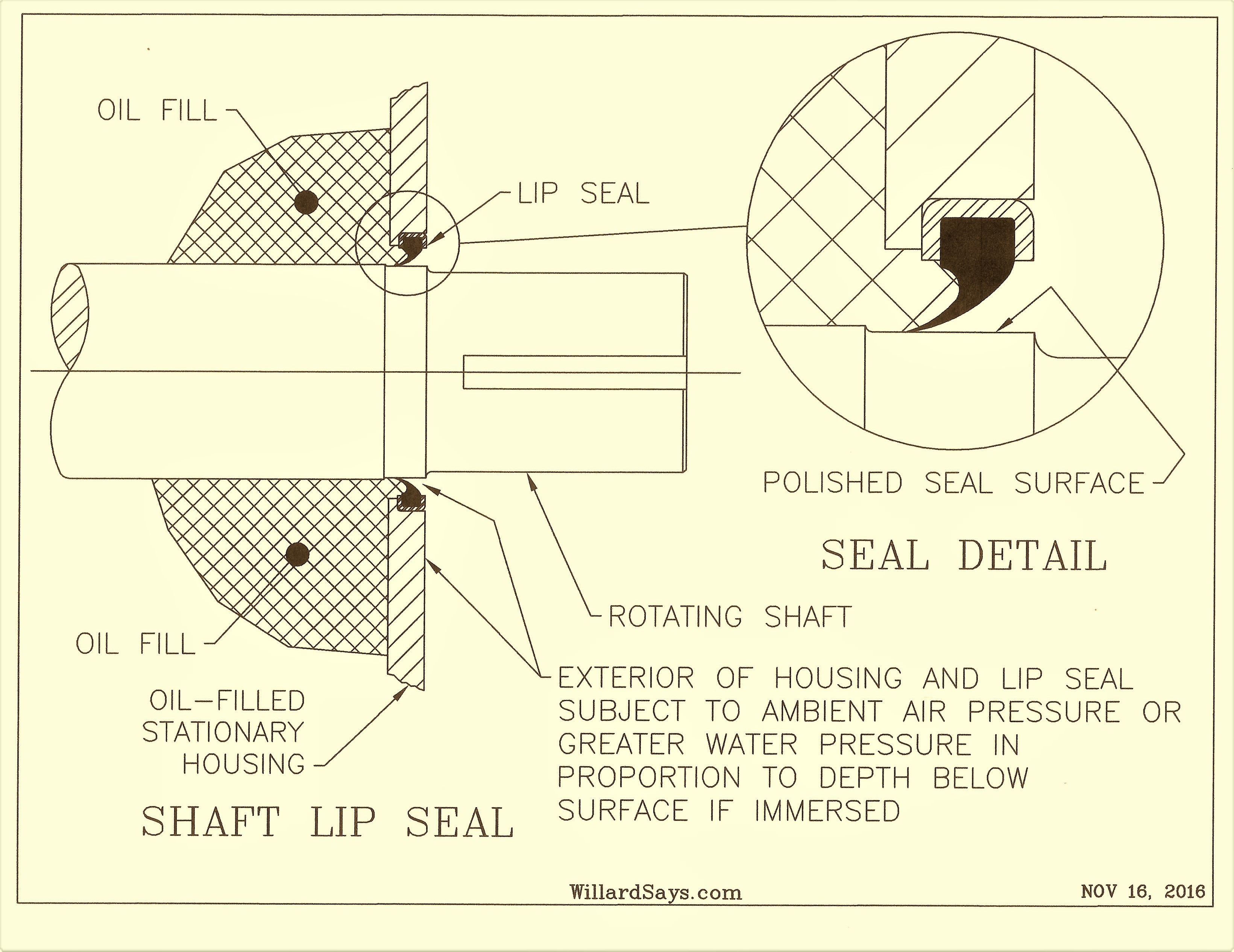
Conclusion: Lip seals are not suited for use in submerged housings.
A Tale from South America
I had an interesting dialogue with a dredger in South America involving static head tanks and lip seals. He builds his own ladderpump dredges and uses most any used dredge pump he can get his hands on, many of them designed to be used above water. He fits the pump shaft bearing housings with lip seals, often several of them. He has tried installing multiple lip sealsāsome facing outward and others inwardāin the effort to keep water out and oil in the housings. None last very long. The longest, about 500 hours. Tearing down and rebuilding a pump shaft housing every few hundred hours is burdensome to say the least. I encouraged him to try metallic face seals and dynamic head tanks.
Now we will turn our attention to metallic face seals.
Metallic Face Seals
There are several manufacturers of metallic face seals, however, we find that Caterpillar Duo-Cone face seals are ideal for use in our cutter gearboxes because they are competitively priced and readily available anywhere in the world. Most of the ladder pumps we use are fitted with Duo-Cone seals.
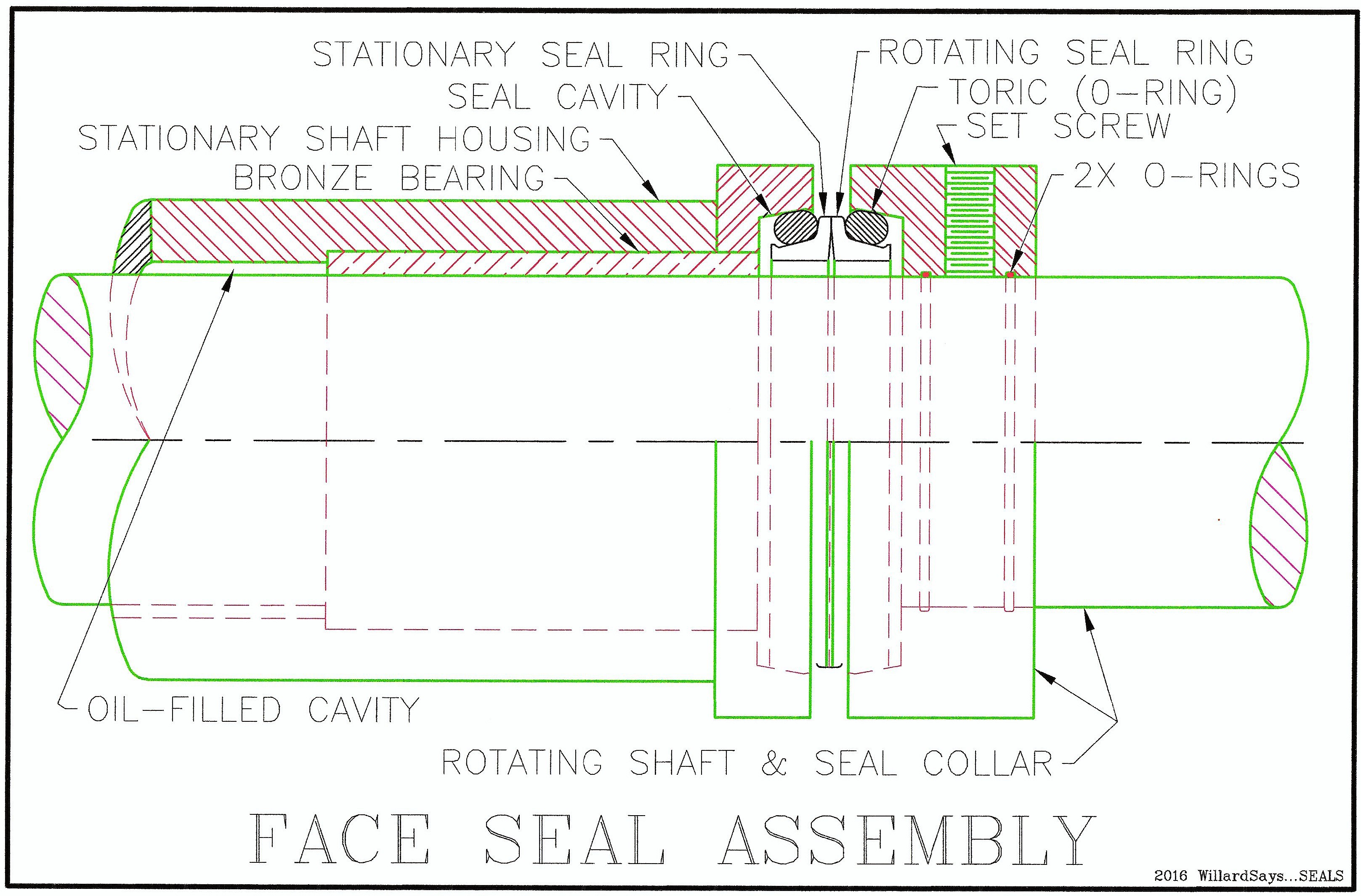
Figure #4 shows a portion of a Caterpillar brochure that explains some of the features of their Duo-Cone metallic face seals. A seal assembly consists of two identical metal rings with torics. Torics are fat O-rings that, when installed in specially machined cavities (one stationary, one rotating), keep the rings aligned with each other and force their mating surfaces to remain in contact.
The metal rings are available in numerous alloys with an assortment of torics with diverse flexibility and thickness. The goal is to tailor the seal so it will function under fearsome conditions.
Figure #4
Metallic face seals are commonly used in two applications on dredges, the high speed, large diameter dredge pump shaft and the low speed cutter drive shaft. These seals are much more robust than lip seals and offer protection even when the pressure gradient across the seal is negative, however, it should be noted that eventually this seal is designed to wear with use; worn out it will leak.
Caterpillar says, āa simple visual check shows the amount of remaining life.ā This is wishful thinking because a dredger who tears his pump down occasionally to ascertain the condition of its seals is a very rare bird. Tear down is done only when it has to be rebuilt after water has intruded and ruined the workings.
Long operating life can be obtained if the lubricating oil is changed periodically and kept free of water contamination by maintaining a positive pressure across the seal.
Positive Differential Pressure
Positive differential pressure across a shaft seal describes the condition where the oil pressure inside an oil-housing is always higher than the water pressure lurking on the outside of the housing.
How can that condition be obtained and maintained? The answer is use a head tank. Two versions of these systems are examined in the following papers.
See WillardSays….Static Head Tanks for relatively shallow applications.
See WillardSays….Dynamic Head Tanks for applications fifty feet and deeper.
Contact willard@willardsays.com with questions, comment or criticism.