Willard SaysâŚâŚ
Winch Installation affects performance of the winch, hence, performance of the dredge system. Improper installation will prevent a winch from serving its intended purpose. After a winch with the desired mechanical features is selected to develop a certain linepull, inhaul cable at the desired speed and spool the necessary amount of cable, it must be properly installed so that it can operate at full capability. Proper installation assures that the winch will operate with a minimum of problems.
ALIGNMENT
The winch must be mounted so that its drum shaft is at a 90-degree angle relative to a line that extends from the center of the drum to the first sheave. Failure to align the winch will prevent the cable from winding onto the drum as it should. See more below under âfleet angle.â
It is a rare application where a cable extends directly from the winch drum to the actual load. Successful operation of such an arrangement requires that the load always stay aligned relative to the winch drum.
The common arrangement is for the winch cable to leave the drum and go through a fixed sheave block, which we will call the âfirst sheave.â Coming out of the first sheave, the cable goes on to another sheave or to an anchor or other load. Causing the cable to go through the first sheave before it goes elsewhere makes it possible to achieve and maintain winch drum alignment. The sketch below shows the proper arrangement.
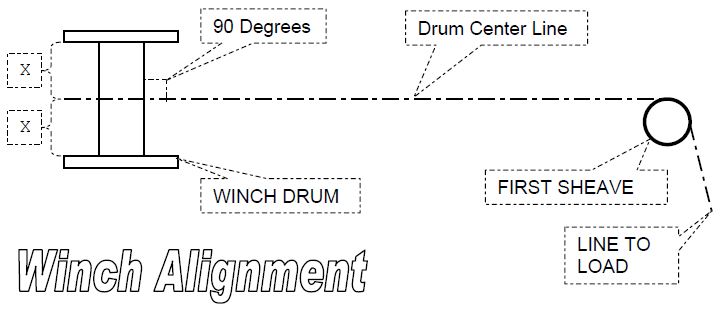
If the cable piles up on one end of the drum it is misaligned. If cable piles up in the middle of the drum it is likely that the fleet angle requirement has been abused.
FLEET ANGLE
is the angle between the tensioned cable as it extends from either end of the winch drum to the first sheave relative to a line that extends from the center of the drum to the first sheave. If the fleet angle exceeds about 1.5 degrees it is likely that the cable will not spool onto the drum in uniform layersâthe cable will âpile upâ on the drum. Improper cable spooling leads to ânesting.â The cable should wind onto the drum and fill it from end to end building layer on top of layer.
Nesting is the name for what happens when heavily tensioned cable knifes down through loosely wound or âpiled upâ underlying layers and wedges into place. Consequently the nested cable will not pay off the drum and must be freed by the frustrated operator.
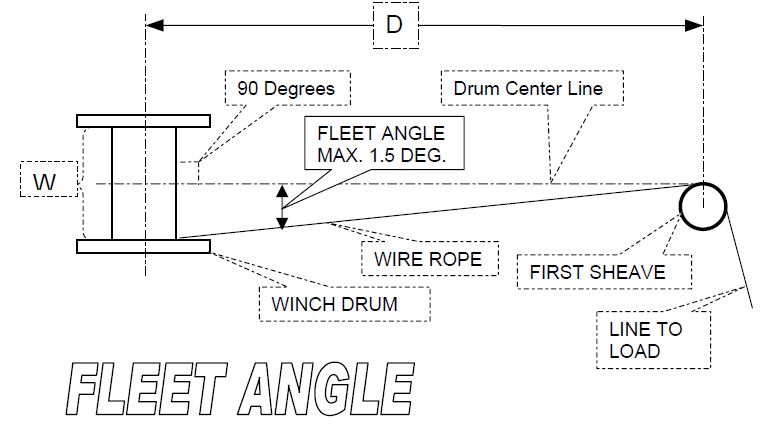
The fleet angle depends on two factors as shown on the above sketchâthe width of the winch drum (W) and the distance between the drum and the first sheave (D). The chart below can be used as a guide to determine the minimum distance (D) that corresponds to a fleet angle that will not exceed 1.5 degrees for various winch drums (W). Distance (D) is a minimum. There is no limit to the maximum distance (D).

SHIMMING
Winchesâespecially planetary winchesâare relatively fragile collections of steel parts until they are firmly bolted into place. If the parts are forced out of alignment, oil leaks, slipping brakes, erratic operation or perhaps serious damage to internal parts is likely to result.
Bolting a winch down on a mounting surface that is not absolutely flat will distort the winch and cause misalignment problems.
Assume that the winch has been checked for alignment and is ready to be bolted to its rigid mounting base. The mounting bolts are fitted into the holes. In a perfect world the mounting pads on the base will be milled perfectly flat so that the winch is setting foursquare on the base with each corner mounting foot in solid contact with the base. If that is the caseâbolt the winch down.
If a winch can be teetered on its base it indicates that only three of its four mounting feet are in firm contact with the base. This is a normal situation and the solution is to install shims into the gap between the âhighâ foot and the base.
Tighten the three mounting bolts that are resting firmly on the base and measure the gap between the high foot and the base. Loosen the three mounting bolts, place a shim of proper thickness under the high foot to fill the gap and tighten and torque all the bolts. The winch should now be setting foursquare on its base, free of stresses that would tend to twist and force the winch assembly components out of alignment.
BRAKE CHATTER
It is not uncommon for a planetary winchâespecially a ladder hoist winchâto âchatterâ when lowering the ladder. Chatter describes what happens when the winch brake grabs and releases in rapid repetition under heavy load. Chatter stresses all of the rigging components and the ladder structure. Carefully read the winch manufacturerâs installation literature, especially as it relates to the size of the hydraulic supply and case drain lines. In some cases the routing of the case drain line may be critical.
Let us know if your winch still chatters even after applying all of the solutions suggested by the winch manufacturer.
All of the chattering winches of our acquaintance are now running smooth as silk. We can help you put the smooth on your winch too. |
WINCH DRUM CAPACITY
The formula, sketch and chart below will help you determine how much cable of various sizes will spool onto a given winch.
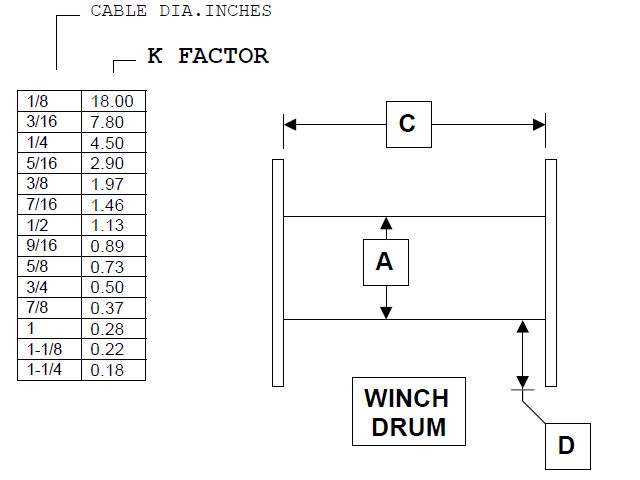
Use the formula: Drum Capacity in feet = (D + A) x D x C x K Factor for cable size
Example: How much 5/8â cable will spool onto a drum with the following dimensions: K = 0.73, A = 10.0â, D = 4.5â & C = 14.0″
Drum capacity = (A + D) x 4.5 x 14.0 x 0.61 = 14.5 x 4.5 x 14.0 x 0.73 = 669 feet.
Safety considerations dictate that the drum should not be filled above the top of the flanges. Regulating authorities may require that a half-inch of flange protrude above the top layer of a full drum. Reducing the dimension âBâ by one half-inch shows that the safe rated capacity of this winch drum is to be about 572 feet of 5/8â cable.
Winch manufacturers require that a minimum of four wraps remain on the drum at all times in order to develop the rated pull of the winch.
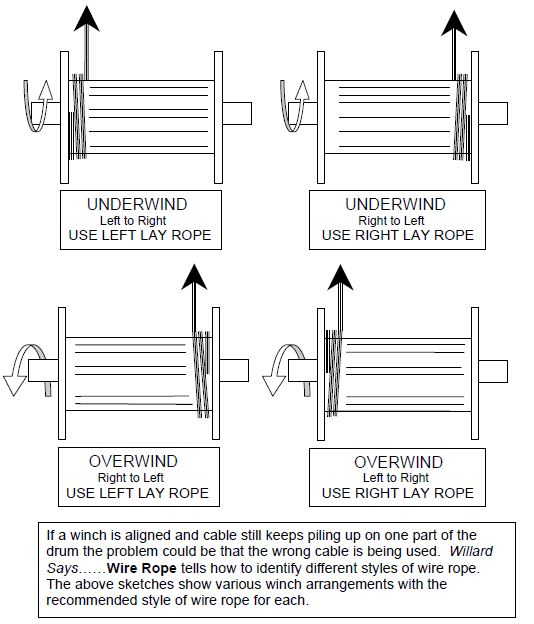
Comment, question, criticism, information on products mentioned? Contact willard@willardsays.com.