Willard SaysâŚâŚ
Three-Wire Positioning is probably the most popular, least expensive and most productive arrangement for mooring and maneuvering a sand and gravel dredge. Three anchors properly arrayedâ one behind and two aheadâprovide the operator with great freedom of movement: the better to maintain peak production.
As shown below three winch-powered cables, right and left swing lines and a tail line, locate the dredge. The discharge pipe is fitted with at least three flexible joints and kept sufficiently long so that it has to form a “dogleg”. The dredge can back up or move forward and dig sideways as it swings on a radius. The discharge pipe is lengthened in 50-to-100- foot increments as required to maintain the “dogleg”.
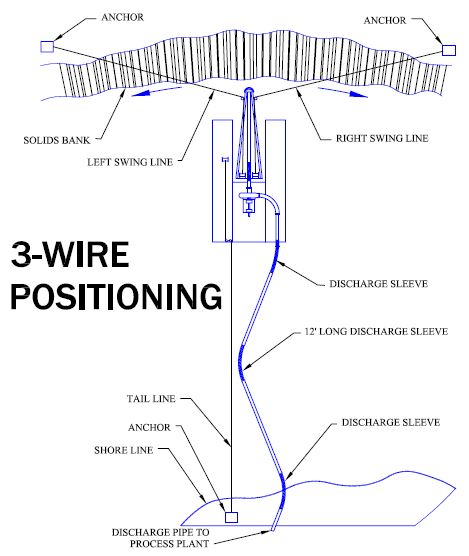
If the dredge is to have full maneuvering capability, it must be able to move forward and backward and the pipeline must have flexibility to accommodate this movement. Three flexible joints as shown on the sketch are a minimum to achieve a dogleg arrangement. Additional joints may be necessary if the discharge line is very long or other special conditions exist. Plastic pipeline provides the needed flexibility without requiring sleeves or balljoints.
Winches
The positioning winches must have easy-to-operate remote controls located at the operator’s fingertips. Hydraulic winches are preferred because they can be “feathered” to accomplish frequent, small movements.
The start-stop, bang-bang operation of electric winches contributes to jerky, unsatisfactory operation.
Likewise, air or hydraulic operated friction winches are not recommended.
Winches should have line speeds of less than 150 feet per minute and should spool at least 300 feet of wire rope.
Just Say NO To Contract Dredging Procedures
Willard SaysâŚâŚPositioning Systems explains how procedures for mining sand and gravel differ from those used by contract dredgers. Contract dredgers feed the cutter/suction inlet by swinging in an arc about a fixed pointâa stake in the groundâcalled a spud. They commence cutting from the top of the material and work down to the bottom of the deposit in successive swings or passes.
Often the contract dredge cutter âcutsâ while swinging in only one direction so the dredge has to âdeadheadâânot produceâwhile swinging back to start the next cutting pass. We preach the gospel of continuous production: productus non-interruptus. Contract dredging procedures: cutting only one direction; stumping around on spuds; intermittent production. There has to be a better way.
Contrast the contract dredging constant-rate-of-swing technique with the recommended sand and gravel mining procedure; that of keeping the suction inlet at the bottom of the bank of solids. Mining from the bottom of the deposit causes all the various particle sizes to mix as they tumble down to the suction inlet. The goal is to create slurry with a uniform mixture of solids particles to feed into the process plant. Effective sand and gravel mining, as with contract dredging, calls for the rotary cutter to be swung in an arc on a radius determined, not by a spud, but by the length of a tail line.
Note that the speed at which the sand and gravel dredge moves sideways in an arc is no way comparable to the speed at which a contract dredge is swung. Sand and gravel dredges crowd sideways in incremental, small movements measured in inches in response to the need to maintain vacuum at the desired value. The swinging movement is notâcannot beâ continuous. The goal is to undercut the bank and cause cave-ins. Large, middle-size or small cave-ins occur at irregular intervals which frustrates attempts to automate or establish a uniform, continuous swing rate. Automated dredgesâthe ones I have seenâdo not produce at rates worth writing home about.
Maximum production is achieved by crowding the cutter into the solids bank to continuously maintain an ample supply of pumpable solids at the suction inlet in response to the need to hold a high vacuum. The CONVAC modulating bypass valve makes achieving and maintaining maximum production a piece of cake. This system make it easy to maintain vacuum at the desired high value as long as the suction inlet is immersed in pumpable solids.
If you have your heart set on automation, check out our linear cutter dredges equipped with CONVAC and LCAP systems. This combination automates production at a rate that is worth writing home about.
Digging Procedure
Lower the cutterhead until it is in contact with the solids bank and allow it to dig down approximately one half the cutterhead basket diameter. If the cutterhead is allowed to dig down too far it will soon be unable to loosen more material because the ladder frame or suction pipe will “heel” or come to rest on the material which prevents further downward movement.
The vacuum gauge reading is the best indication of when and how much the cutterhead must be moved. Experience will determine what vacuum reading will result in the desired rate of production.
See Willard SaysâŚ..papers on vacuum and velocity.
After the ladder is lowered, commence digging sideways in a arc by pulling in one swingline and playing out the opposite swingline. Tension on both swinglines must be sufficient to hold the cutter against the solids bank and keep some tension on the tail line. The tail line need not be kept “fiddle string” tight. The tail line length determines the digging arc radius.
Continue the sideways digging movement at the rate required to maintain the desired vacuum reading. If the swing winch stalls in the attempt to swing the cutterhead, pick it up a short distance and try swinging again. Once sideways movement has occurred, allow the cutterhead to dig downward until it is back at the previous depth. The objective is to excavate a trench of uniform depth in an arc. Continue to dig sideways to the limit dictated by the location of the swing anchor. When the limit of the swing is reached, advance the dredge.
Short advances are key to successful cutterhead dredging. Play out only two or three feet of tail line whenever an advance is required. Mark the tail line with a piece of cloth or tape and experiment with different advance distances. Continue to use a marking system so that the most productive advance distance can be accurately repeated each advance. Short advances cause small cave-ins.
After advancing the dredge commence cutting an arc in the opposite direction.
Lower the cutterhead after each advance if it is desirable to increase the digging depth. Strive to keep the cutterhead at the desired digging depth once it has been reached so that a “floor” is established and maintained. Cave-ins may require that the cutterhead be raised to reduce vacuum or accomplish swing but always work the cutterhead back down to the “floor” level.
May the Force Be With the Cutter
Warning! It is tempting to move the swing sheaves from the sides of the ladder to the ends of the front pontoons because the operator keeps winding the cables in the rotary cutters. Donât do it! The pull of the swing cables must be applied near the cutter basket to cause it to move into the solids bank. Pulling sideways on the end of the pontoons torques the hell out of the dredge structure. Most of the force exerted with the intent of forcing the cutter into the bank is dissipated before it reaches the diggerâunless something breaks first.
I heard one suggestion on how to stop the cable-in-the-cutter problem, âTell the operator that the first time he snarls the cable in the cutter he gets to use the boat to clear the line: the second timeâno boat.â
Benefits
Three-Wire Positioning yields several positive results:
- Short advances provoke small cave-ins. Often these cave-in require little or no reaction by the operator. The increase in vacuum will not be great and will not cause an interruption in production.
- Short advances and small cave-ins provide the benefit of safety. Long advances can result in cave-ins that may bury the ladder to the extent that it cannot be raised.
- A precise pattern of digging improves the yield of the deposit by enabling more complete recovery of the material.
- A set pattern of digging results in less operator effort to maintain high production. The number of gauge readings which the operator must evaluate and act upon is greatly reduced if he has the means to obtain a desired vacuum reading and maintain it. Most other readings will not change significantly if the vacuum remains fairly constant.
The CONVAC modulating bypass valve assures excellent vacuum control without interruption due to cave-ins. This system eliminates interruption due to normal cave-ins and enables the operator to âdial inâ the desired vacuum and maintain it by keeping the suction inlet immersed in pumpable solids.
As a practical matter of safety and uninterrupted production, short advances result in less bank undercut, therefore smaller cave-ins. The dredge is less likely to be stuck fast by large cave- ins.
Effective and efficient cutter-suction dredging requires that an operating procedure or pattern is developed and followed.
Snatch-Back?
In case of a cave-in, the 3-Wire system gives the operator the option of backing away from the slide. We have installed the Snatch-Back system on several dredges. This system provides the operator with an emergency button to push whenever he detects the onset of a large cave-in. A push of the button causes the swing winch brakes to be released and the tail line winch to pull the dredge rapidly backward 30 to 40 feet. The system includes an oversized tail line winch and hydraulic circuitry that causes the tail winch to reel cable in rapidly. The idea is to quickly remove the digger from the area where cave-in material will come to rest.
Many operators cherish the fanciful idea that they can âbeatâ a cave-in by raising the ladder up through a cascade of material that is sliding down on the digger. Snatch-Back moves the ladder back and out of the way more quickly by traveling in the same direction that the cave-in material is flowing. Normal mining can be resumed with only a slight interruption. It works great if the operator pushes the button.
The freedom of movement possible with the 3-Wire system enables the operator to easily back up and recover slides of material that go behind the suction if that is deemed necessary. Usually, the rate of production while âsweepingâ is so poor that the economic justification for cleaning the floor comes up lacking.
Linear Cutters
The 3-Wire Positioning system is ideal for use on linear cutter-equipped dredges. The front cables can be reeved through blocks mounted high up on either side of the hoist frame or from the ends of the side pontoons. The advance distance can be adjusted to suit conditions, however, about five feet is usually about right.
Limitations
The 3-Wire system should work well for linear cutter dredges, however, it may not satisfy the positioning requirements for every rotary cutter, sand and gravel mining dredge. Conditions that may interfere with the effective use of the 3-Wire system could include:
- High banks of solids above the water level.
- Near vertical banks underwater, (non-free-caving deposit).
- Tough digging conditions.
- Very shallow digging depth.
If one or more of these conditions is causing problems consider installing the 5-Wire Positioning system. It is more complex than the 3-Wire system, but it is very effective in dealing with the problems listed above. See Willard SaysâŚâŚ5-Wire Positioning.
Comment, question, criticism, information on products mentioned? Contact willard@willardsays.com.